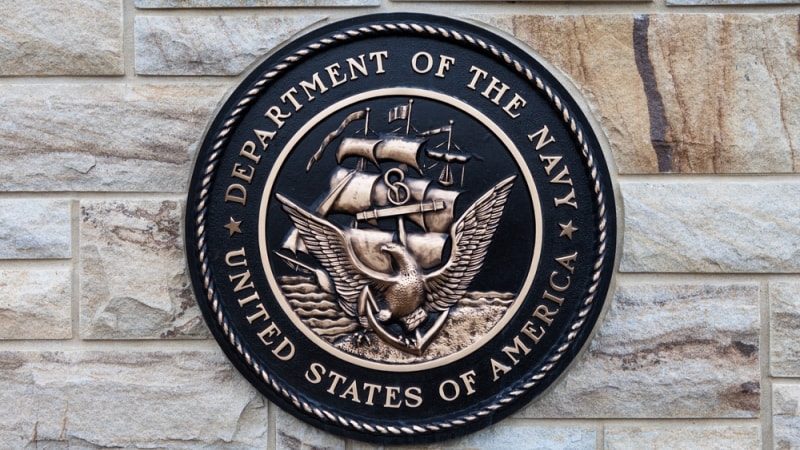
The U.S. Navy is now using artificial intelligence to determine when it needs to take birds out of the air and repair their wings before they get clipped.
The Naval Air Systems Command (NAVAIR) is challenging the conventions of previous aircraft maintenance intervals through AI, in a manner that initially shook the engineering department but now provides early warning of when major systems in the Naval aviation fleet might be starting to fail.
Roy Harris, director of the Aviation Readiness and Resource Analysis Department at NAVAIR, said Wednesday at the Predictive Analytics World Government Conference that AI and data analytics are essentially fueling and refueling that fleet.
The process NAVAIR is using is called “commission-based maintenance,” which “looks at the various conditions that an aircraft has flown,” Harris said. The planes, outfitted with a host of sensors, are now aggressively tracking specific components on the aircraft.
“Through data analysis and developing algorithms, we’re able to assess how much life has been expended on each dynamic component of an aircraft,” Harris said. “Dynamic components are important because they’re time-based: at set intervals they’re due to have certain levels of maintenance performed or be replaced.”
The Navy, in the absence of that sensor data on the planes, geared its maintenance outlook toward worst-case scenarios.
“We had very risk-averse maintenance intervals and time intervals on those dynamic components on our aircraft, that were all kind of dependent upon or predicated on the assumption that the aircraft was always flown in the most rigorous conditions possible,” Harris said. “It’s a little bit of a fail-safe on our part and a risk-averse approach that our engineering community took.”
After Harris’ team operationalized its AI platform and built analytical models based on the sensor data, they began to make informed decisions about the actual wear and tear on the planes.
“We’ve incorporated many different toolsets and many different models that are yielding results that are challenging human assumptions that were made,” he said. “It’s been a little bit of a cultural change.”
“Safety is always of the utmost concern,” Harris said, and what they were now proposing was scary: that they could tone down the amount of maintenance or fly planes for longer than they had in the past.
“For the first time, we’re able to pull the sensor data and actually see how those aircraft were flown, and start to challenge some of those maintenance intervals,” he said. “It was met with a lot of resistance from the engineering community. I mean a lot of resistance.”
His team believed in the quality of the data, but others needed proof. Harris said engineers, before agreeing to adopt any changes, broke down the components, disassembled the planes, and inspected those components.
“We had to go through that probably few turns of the crank,” Harris said, before the engineering community could confirm the findings and finally gained confidence in the analytical models Harris’ department had built. Eventually, they received support to extend the service life on the aircraft. “It was definitely a culture shock,” he said.
And rather than contributing to risk, Harris suggested the new process could be impacting safety on an even broader scale.
“We’re starting to look for indications based on the sensor data of major subsystems starting to wear or fail,” he said. “We’re able to pull those systems and do preventative maintenance before we have a major failure in the fleet.”